Hydraulic Bootstrap Reservoir
How does the process work?
Hydroforming is a manufacturing process which uses a high-pressure fluid to achieve the plastic deformation of metal components.
Specifically, tubes hydroforming is a technology where pipes or specific pre-shapes are expanded from the inside out by means of a liquid working medium in a closed die.
This method makes it possible to manufacture hollow parts with a complex external shape or localized section variations always having components consisting of a single piece. Unlike other metal forming techniques, hydroforming allows for increased part strength, lower part weight, and design flexibility, while also improving overall part quality. In our factory we can count on a 1.000 tons hydraulic press equipped with an injection system able to achieve a pressure up to 2.200 bar.
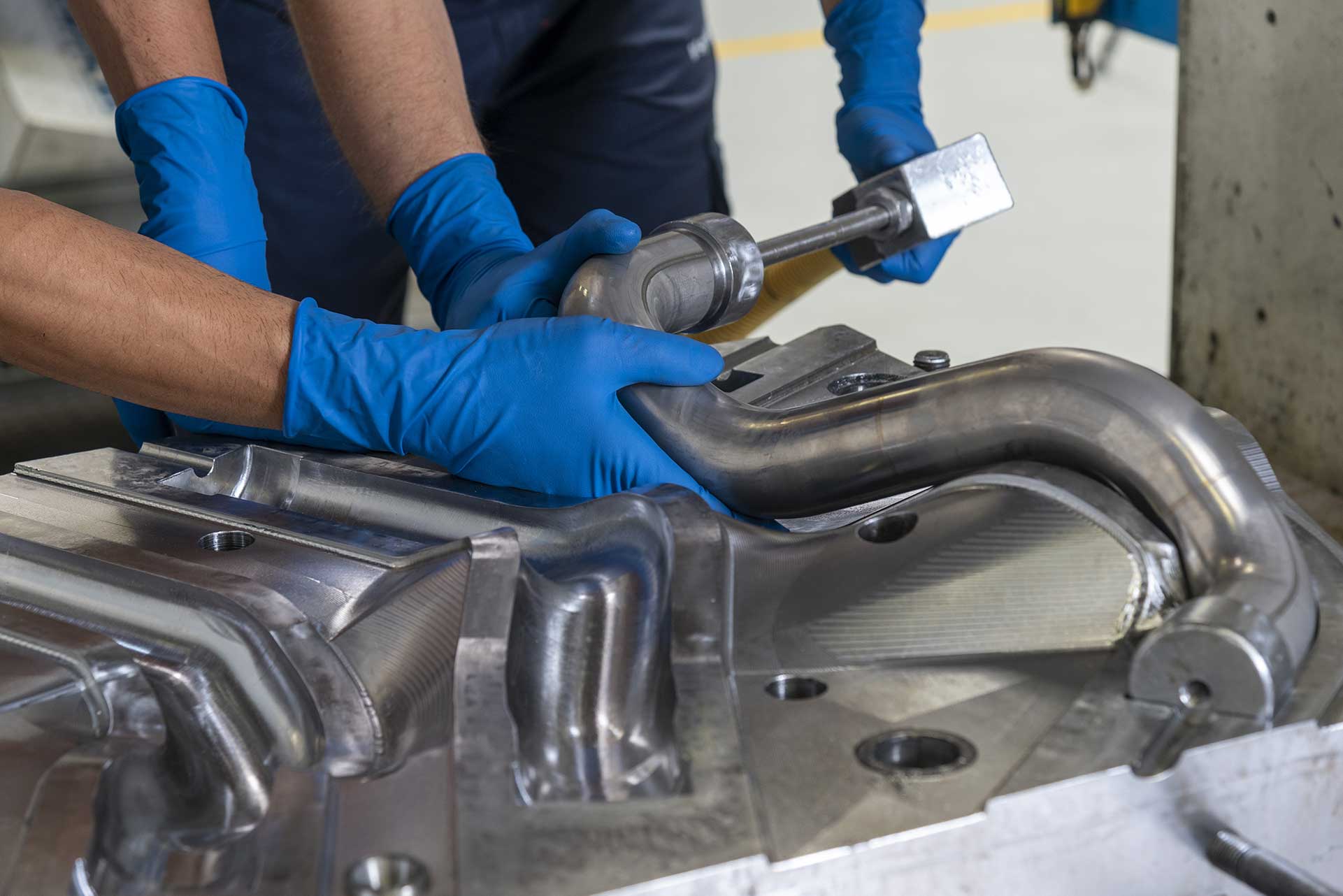
Experience and uses
In recent years, our Company has gained extensive experience in the creation of hydroformed exhaust systems for the motorsport sector and also on other components with extremely complicated shapes.
VSystem team is able to supply any type of hydroformed parts according to the customer's requirements and all the steel matrices needed for the process are fully developed within our R&D office.
Apart from this, we can also perform accurate dimensional and thickness analyses on hydroformed components, specific intermediate and final vacuum heat treatments, NDT testing and customized surface finishing.
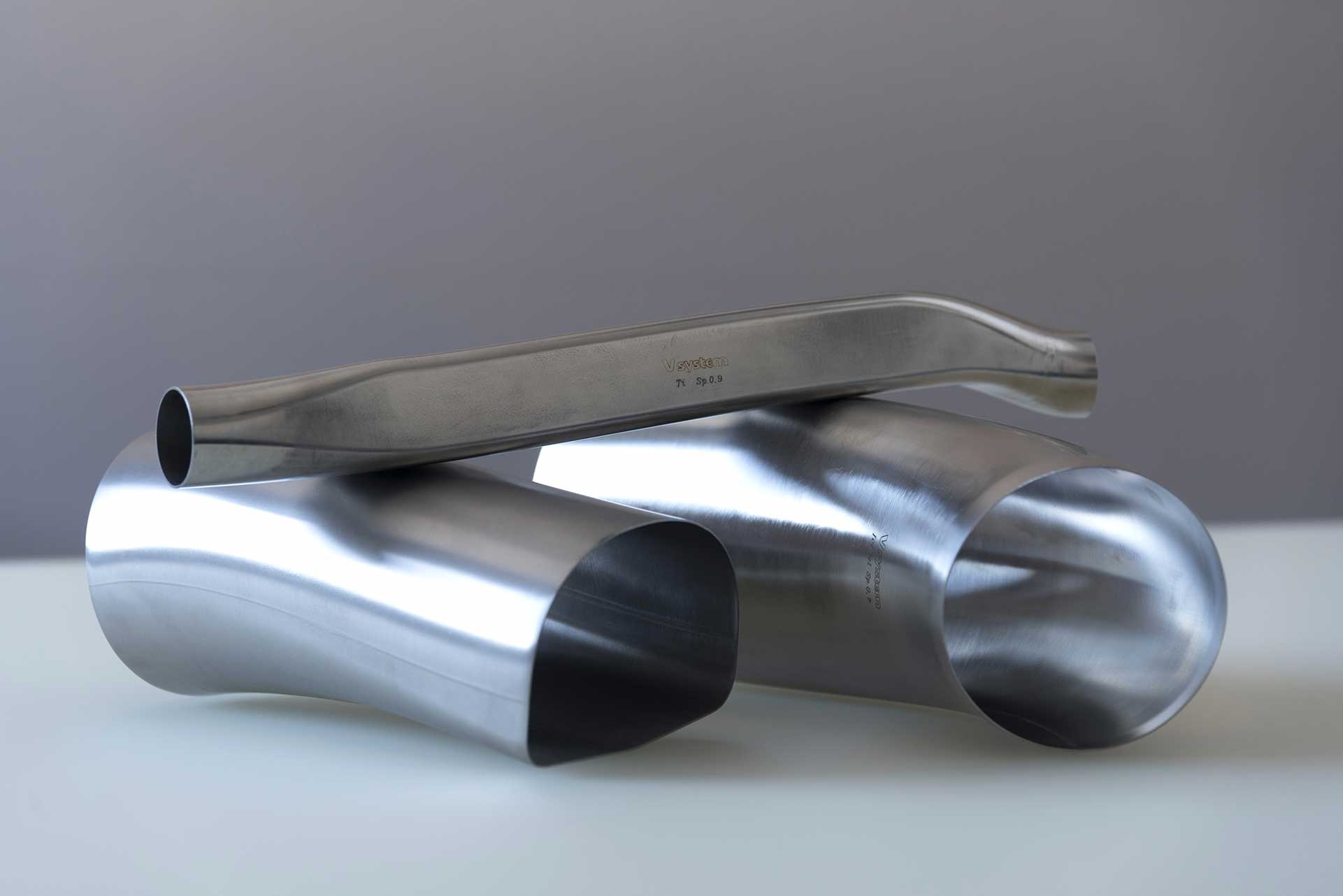